熱可塑性不連続CFRPを用いた鍛造
1.緒言
炭素繊維強化プラスチック(CFRP)は軽量かつ高強度であることから輸送機器を軽量化し、燃費を向上させることが期待されている熱可塑性CFRP(以後CFRTPと呼ぶ)は、短時間で成形できる材料として期待されているCFRTPの内、連続繊維のCFRTPは強度が高いが成形する形状に制約がある繊維を一定の長さに切った不連続繊維
CFRTPとすることで、連続繊維CFRTPより強度は劣るが、多様な形状に成形できる可能性がある。
そこで本研究では、不連続繊維CFRTPとして、一方向炭素繊維テープを所定の長さにカットして圧着させた平板を材料とし、複雑形状部品の鍛造成形を行い、成形挙動や成形条件を解明することを目的とする。
2.成形対象
成形対象をカップ形状の成形品としたFig.1に成形品の3Dモデルおよび断面図を示す。
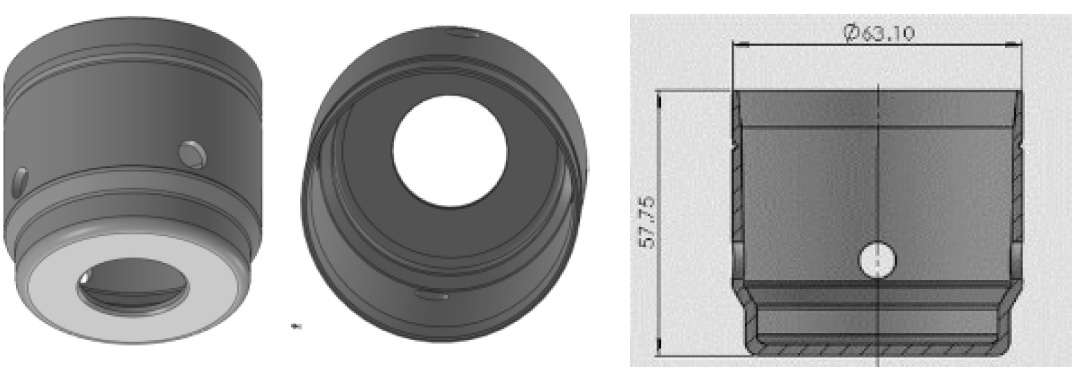
3.実験装置及び実験試料
3.1 鍛造金型
鍛造金型の構造をFig.2に示す。カップ形状の空洞を有した下型にポンチを挿入してカップを成形する。材料は下型の底に置き、ポンチで加圧して後方押出しによって成形する構造とした。下型とポンチにはヒータを内蔵し、CFRTPの母材樹脂の溶融温度近傍に金型を加熱して、樹脂が固化温度まで冷えないうちに成形する。成形後はヒータの通電を切って、自然冷却を行ない樹脂を固化させる。この冷却過程で材料が熱収縮するため、下型のイジェクトピン部分に入りこんだ材料をダイクッションピンで加圧を続けることをねらった。横穴ピンとリング溝ピンはツメが入ることで内側にスライドし、成形する。
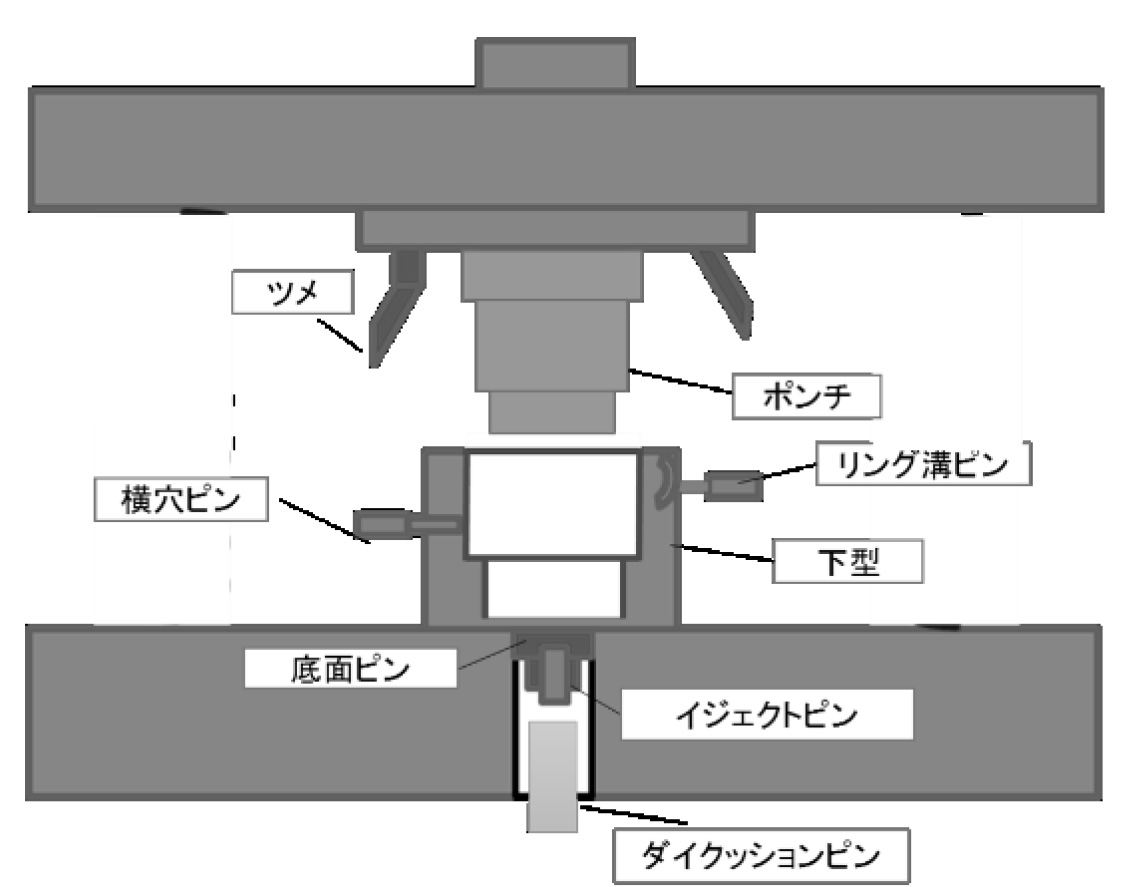
3.2 鍛造材料
鍛造材料として、炭素繊維にナイロンPA6を浸透させたCFRTPのUDシートを用いた。UDシートの厚さは0.16mmで、Vfは50%である。
UDシートには繊維長が30mmとなるようにカットを入れた。カットの方向は繊維方向に対して45度とした。このようなUDカットシートを繊維方向が45度ずつ異なるように積層する。
UDカットシート積層版の成形プロセスは以下の通りである。
(1)UDシートを16枚積層する
(2)重ねたCFRTPシートを加熱した金型に置き、溶融状態まで加熱する。
(3)プレスを行い、CFRTPシートを圧着させる。
(4)金型から成形品を取り出。
成形したUDカットシート積層版をFig.3に示す。
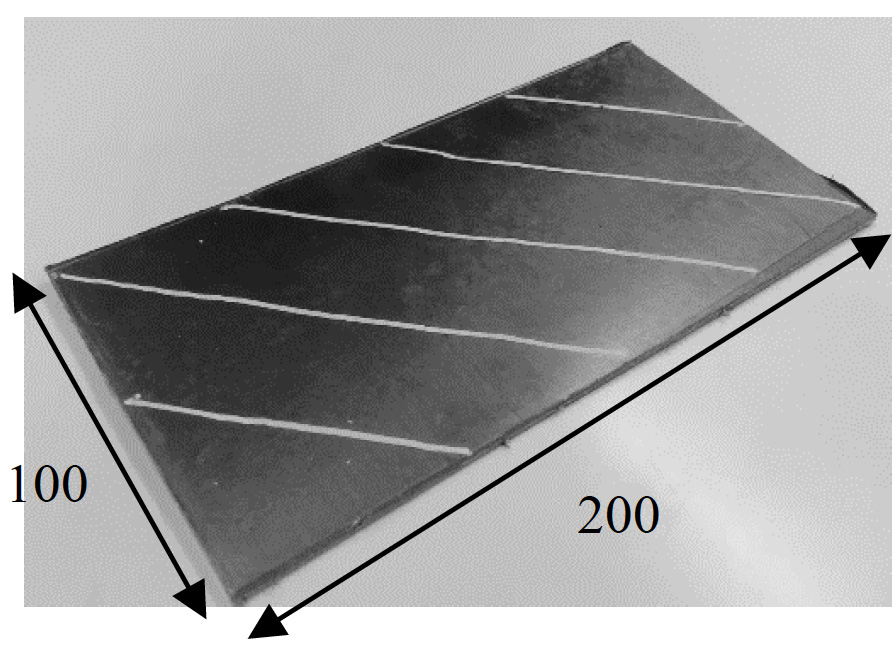
UDカットシート積層板はUDシートを16枚重ねたものでありその中の繊維方向とカット方向はFig.4に示す積層が4回くり返されたものになっている。
UDカットシート積層板から八角形を切り出し、これを8枚重ねて鍛造用の材料とした。
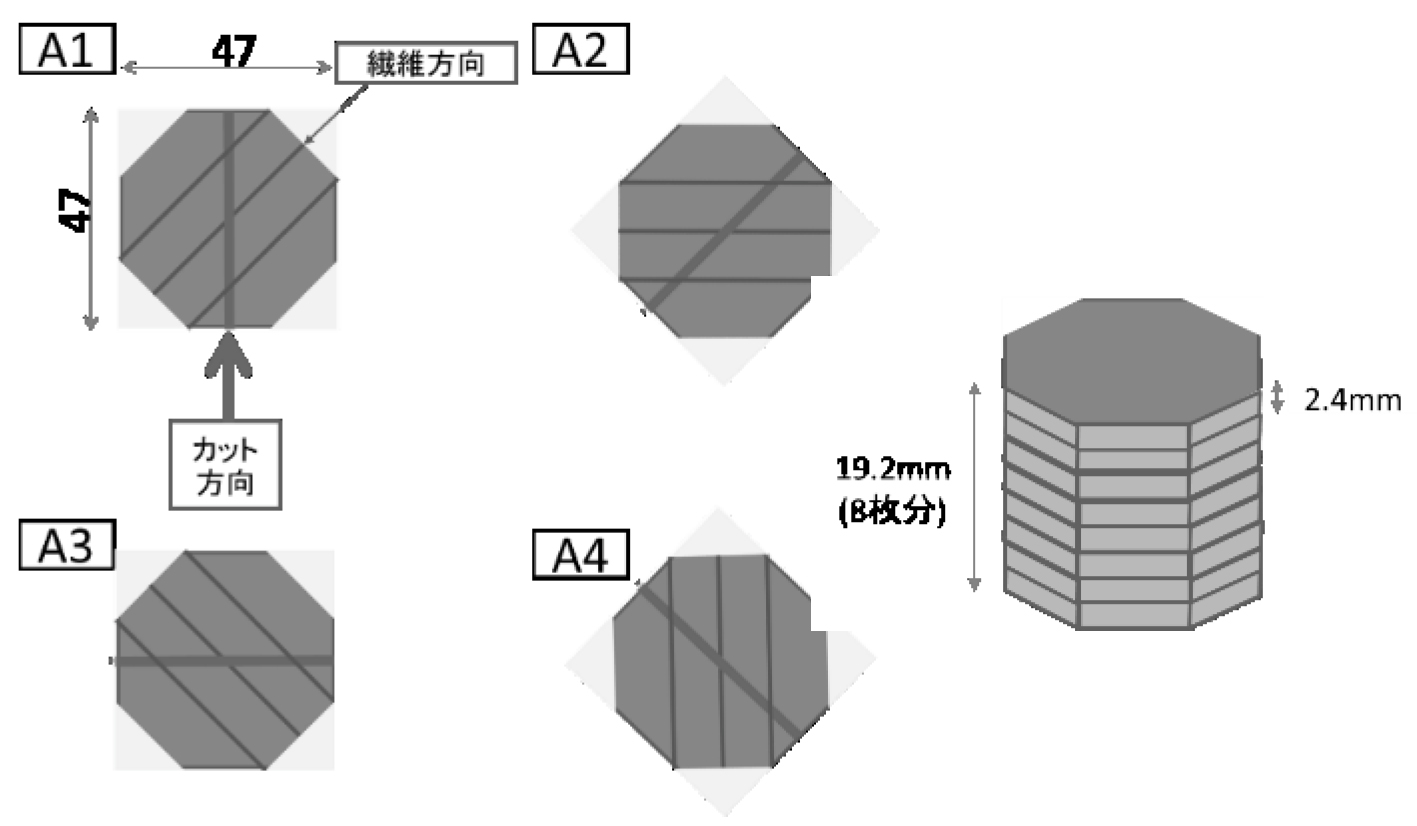
3.3 プレス機
プレス機はコマツ産機(株)製ハイブリッドACサーボプレスH1F45を用いた。ストロークは100mm、最大荷重は450kNである。
4.鍛造成形条件
鍛造成形条件をTable1に示す。成形のプロセスをFig.5に示す。
(1)材料は300のマッフル炉内で280まで加熱した材料を下型に挿入する。
(2)位置制御によってポンチを下げていく。ポンチが材料に接触し材料を流動させていく。
(3)空気圧でダイクッションピンを押し上げ、イジェクトピンをスライドさせる。空気圧は設定した圧力になるまでタイムラグがある。材料を自然冷却し熱収縮がおきたときに更にイジェクトピンがスライドする。
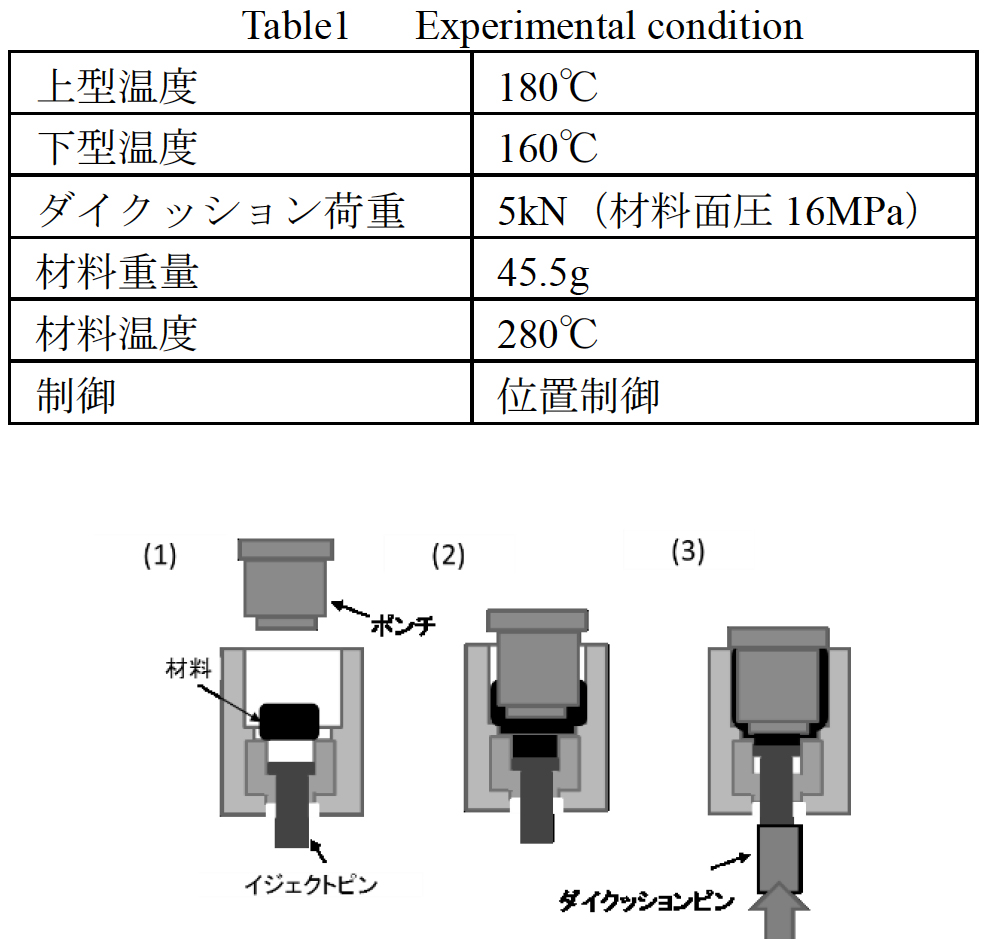
5.実験結果
5.1 成形品外観
成形品の外観をFig.6に示す。成形上部まで充填ができている。横穴上部には材料の合流点が見られる。成形品の外径は設計寸法63.1mmに対して最大外径63.2mm、最小外径62.4mmとなっており歪んだ円になっている。
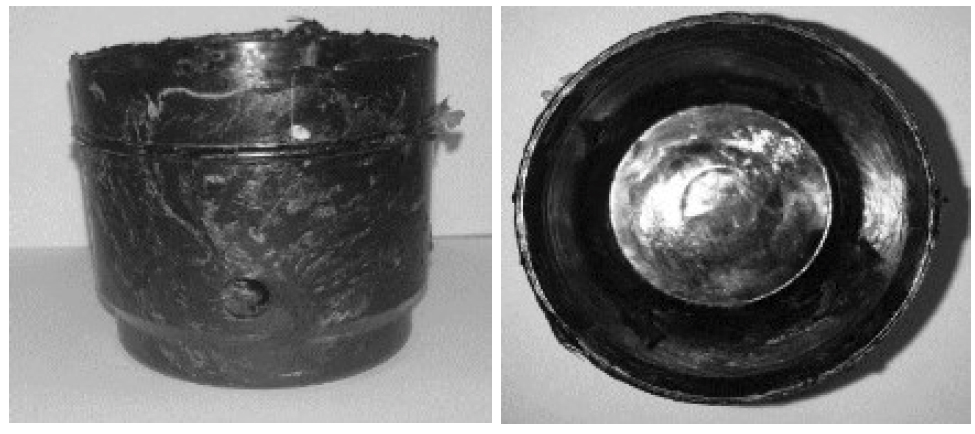
5.2 成形荷重
成形時のプレス荷重・スライド変位・ダイクッション変位の時間波形をFig.7に示す。スライド変位0mmは下死点を示す。
スライド位置が10mmの時にポンチが材料に接触し荷重があがり材料を流動させる。下死点に達したときに最大荷重43kN材料面圧14MPaとなる。荷重ピークを超えた後は再び35kNまで上がり。その後、荷重は徐々に下がっていった。ダイクッションは11.5mmで一度イジェクトピンに接した後にダイクッション荷重が5kNまで上昇する過程で14mmまで上がる。6s以降は材料の熱収縮に伴い15mmまで上昇したと考えられる。
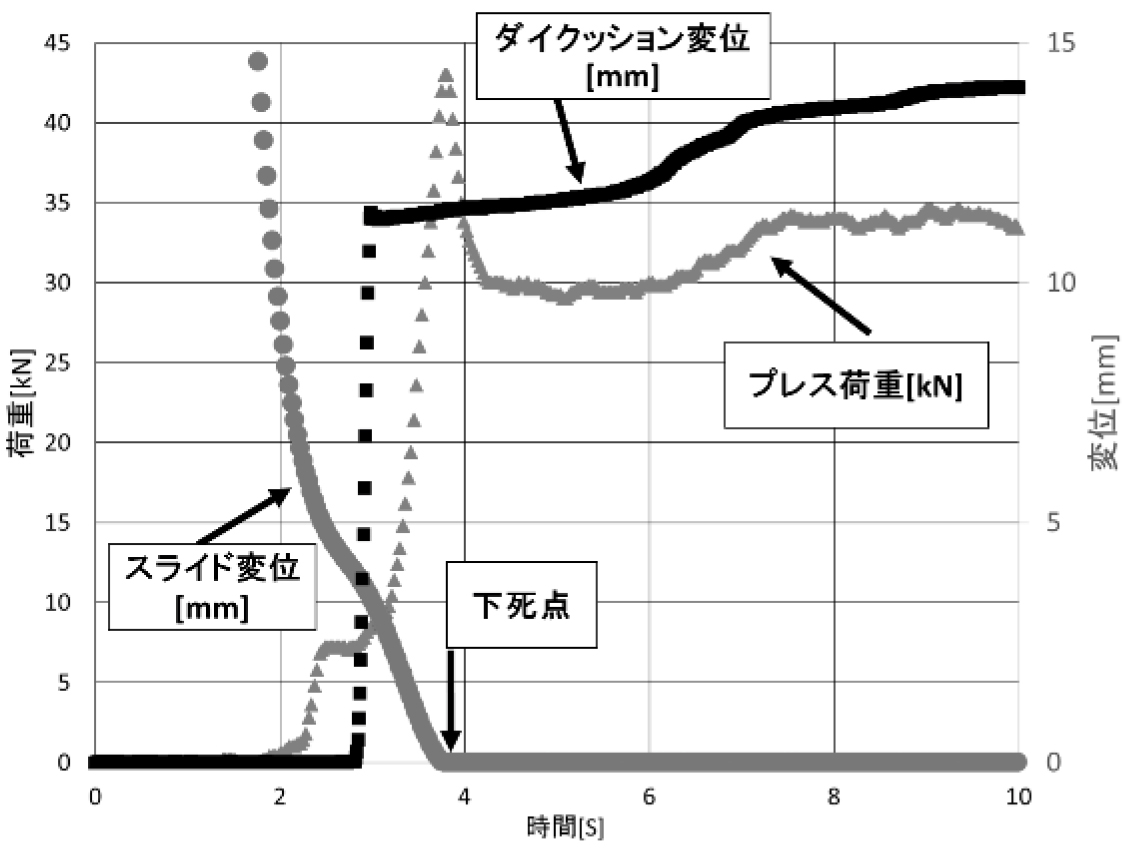
6.成形品断面観察
光学顕微鏡を用いて成形品のリング溝断面、横穴上部断面、コーナー断面の観察を行った。断面観察位置をFig8に示す。断面写真をFig9に示す。
リング溝上部には屈曲した流動が見られる。上部に材料が達した後も押し込まれ続けたと考えられる。
横穴上部には断面に対して垂直の炭素繊維と平行の炭素繊維の層が積層されている事が確認できる。
コーナー部には屈曲した流動が見られる。
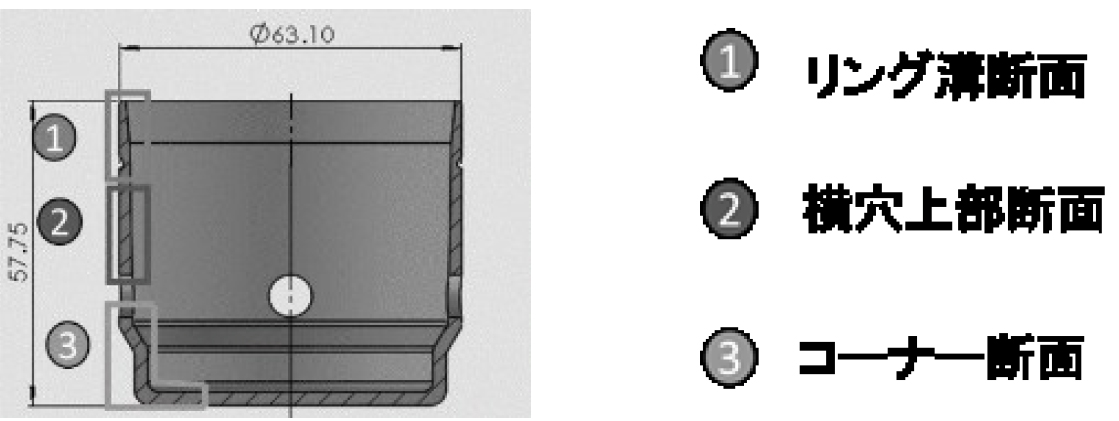
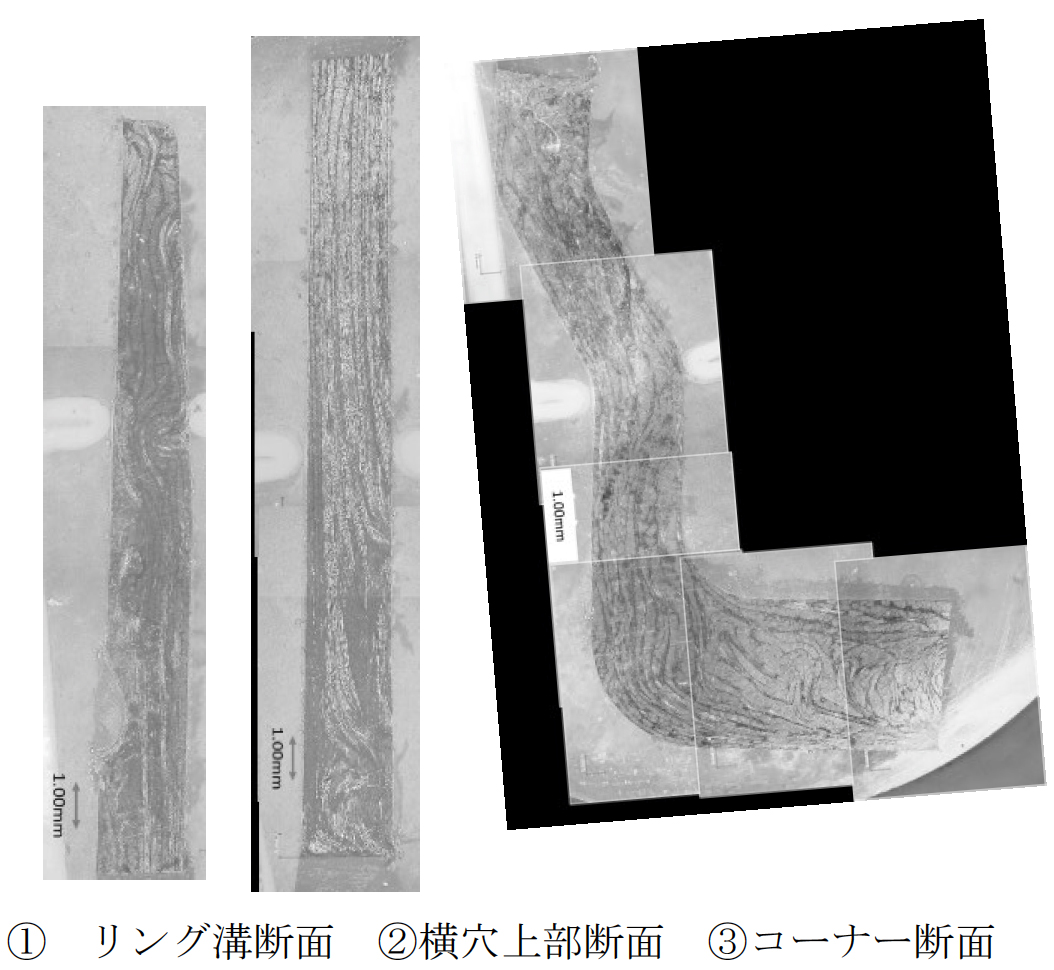
7.結言
CFRTP一方向炭素繊維を所定の長さにカットして繊維方向を変えて圧着させた平板を材料とし、複雑形状部品の鍛造成形を行い、成形品を充填させることができた。
光学顕微鏡を用いた断面観察により成形品内部の材料流動と積層を確認した。今後成形品強度試験を行う。
本研究に対し、天田財団より助成を受けた。
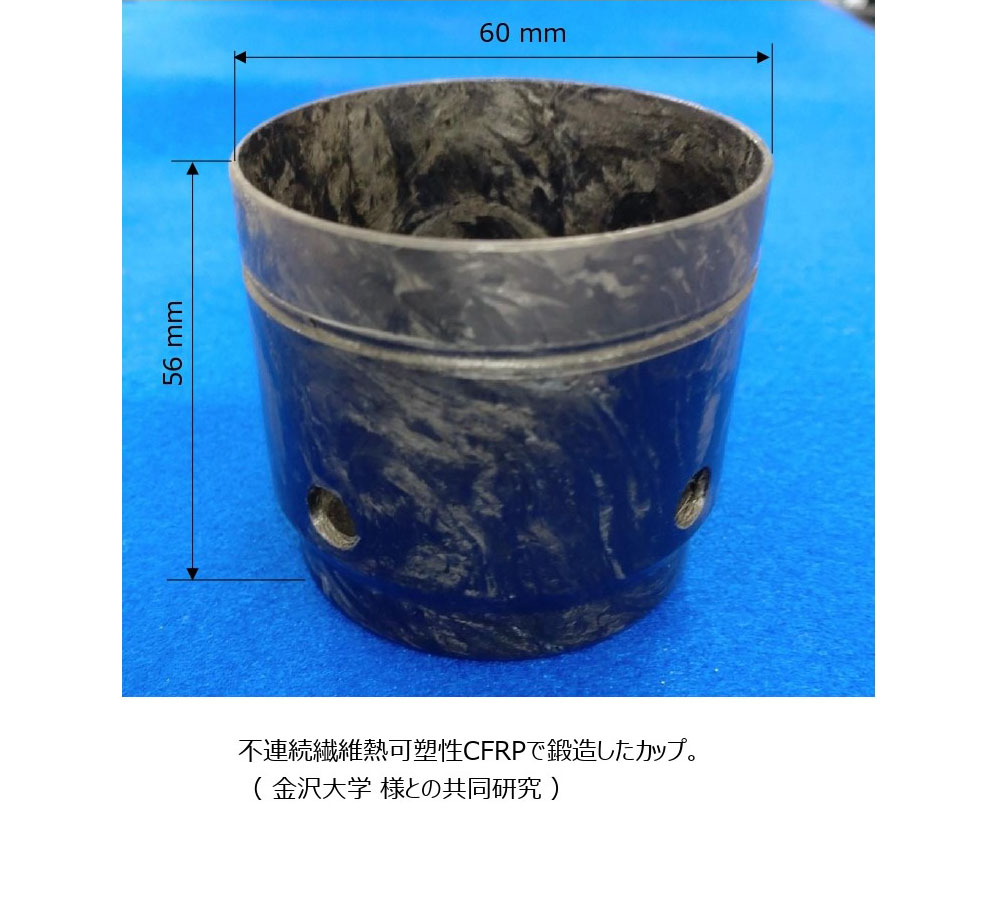
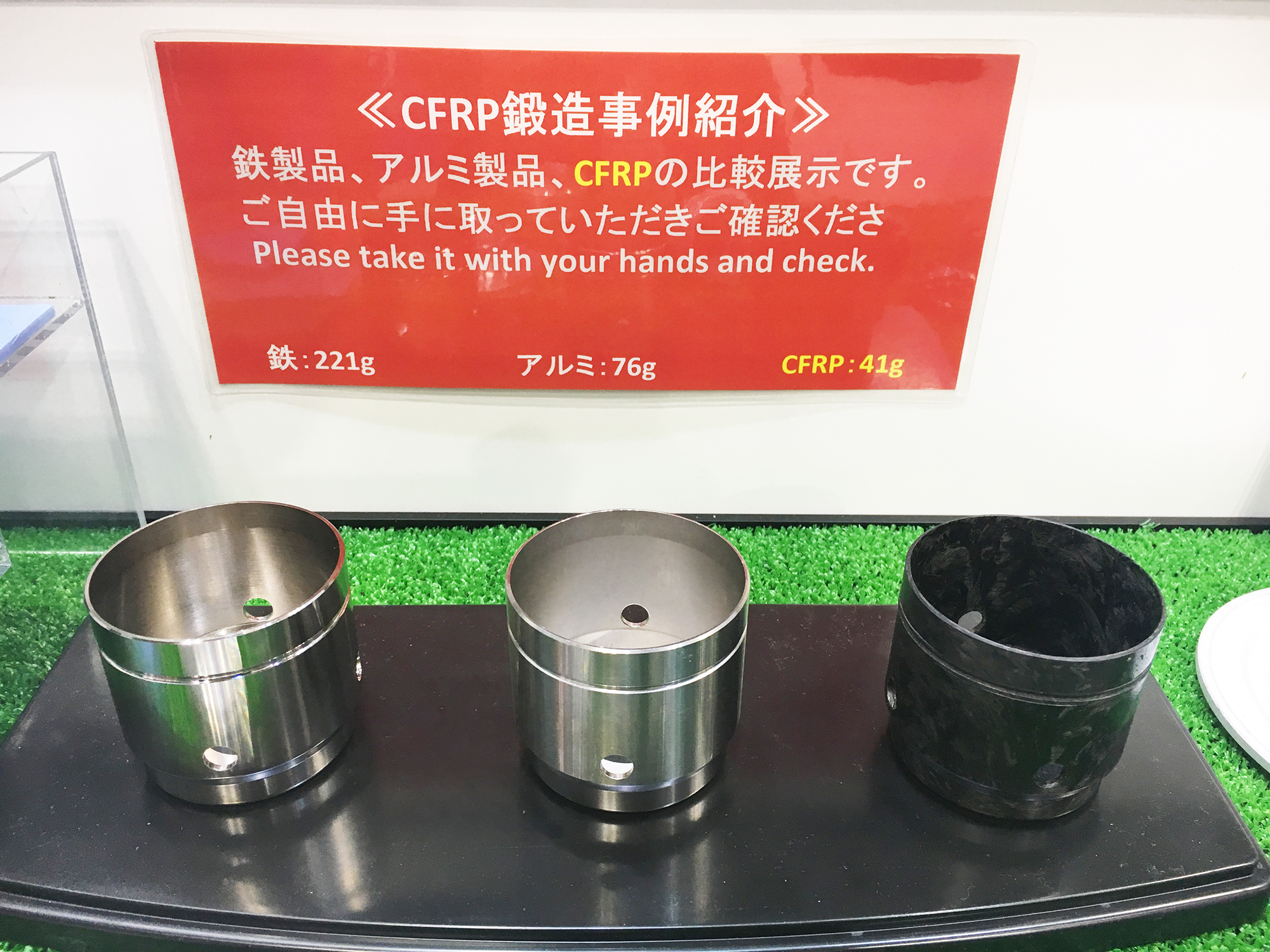